CHEMICAL REACTOR DESIGN
A chemical reactor is most often a cylindrical vessel within which the chemical reaction between two or more chemical compounds or substances takes place. The primary features in a chemical reactor design comprises of an agitator to provide mixing, electric motors and gear boxes to drive the agitator, a jacket or an internal coil through which the heating or cooling medium is made to flow, necessary sealing arrangement for the shaft of the agitator to prevent unwanted leaks, structural supports for the chemical reactor and thermal insulation to prevent loss or gain of heat from outside atmosphere. While stirred reactor design as above function as batch reactor or even as continuous stirred tank reactors (CSTR), tubular reactors are generally used for reactions in continuous mode. Circulation of heating or cooling medium through the jacket or coil in the reactor design helps in supplying or removing the heat from the reaction mixture.
Reactor design has another technique which helps in conducting the reaction which is known as adiabatic reactor design .Designing involves determining the type and intensity of agitation required, removal or supply of the required amount of heat in order to maintain the optimum temperature conditions for the reaction, etc.
REACTOR DESIGN & OPTIMIZATION OF HEATING AND COOLING SYSTEMS:
Chemical Process Engineers specializes in Reactor Design which involves optimization of heating and / or cooling systems to maintain precise reaction conditions, faster reactions to maximize production capacity, minimum energy wastage and best utilization of reactor capacities.
Reactor Design and optimization of systems are carried out by:
- Arrive at the quantum of thermal energy that should be supplied or extracted from a given batch during its progress. This is based upon stoichiometric analysis of the reaction of the reactor design.
- Maintain high heat transfer coefficients in the reactor to promote increased rate of heat transfer.
- Maximize the surface area availability of transfer of heat.
- Maintain optimum intensity of agitation to ensure uniform mixing and also to maximize the inside heat transfer coefficient and bring it at par with the jacket side heat transfer coefficient.
Reactor heating/cooling systems are designed by the following :
- Maintain high heat transfer coefficients in the reactor to promote increased rate of heat transfer.
- Maintain low temperature differential between reaction mixture and thermic fluid in jacket to minimize loss of yield in case of heat sensitive products.
- Rather than circulate thermic fluid through jackets of every reactor at the same temperature, provide thermic fluid for respective reactor design at the most optimum temperature.
- Recirculate thermic fluid in a closed loop around each reactor design with introduction of hot fluid into the loop through specially selected three way valves.
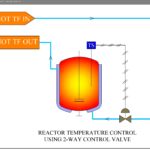
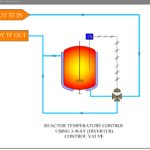

For those reactions that are not constrained by the kinetics, special features are designed to enhance the heat transfer area which speeds up the process and hence promotes higher productivity.

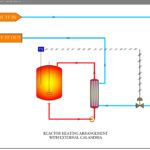
Separate cooling circuit is provided for quick cooling of any reactor design and prevents cooling down of the entire bulk of hot thermic fluid in the hot oil circuit that results in considerable energy loss.
Thermic fluid heaters are designed and tailor made for reactor design and heating applications to operate at 95 % + thermal efficiency on gas. These heaters operate on the principles of counter-current heat exchange with hot flue gases generated from consumption of LPG and controlled recycle of hot exhaust air
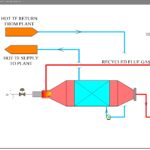
Thermic fluid heating systems are also designed with secondary and tertiary loops to cater to multiple equipments requiring flowrate in the circuit higher than what a standard heater provides for.
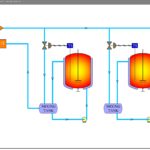