ANALYSE & OPTIMISE YOUR DRYING SYSTEM TO REDUCE DRYING COST FOR
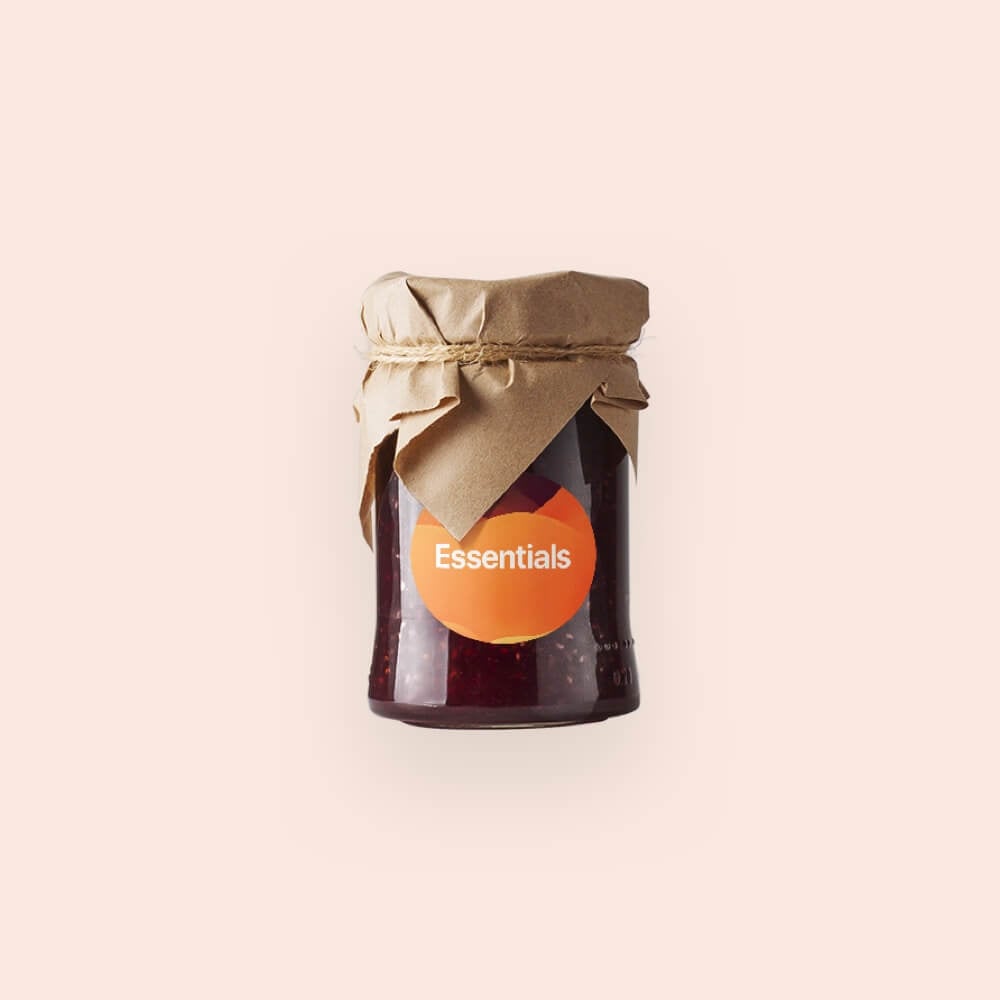
Counter-current, rotary continuous drying of granular materials
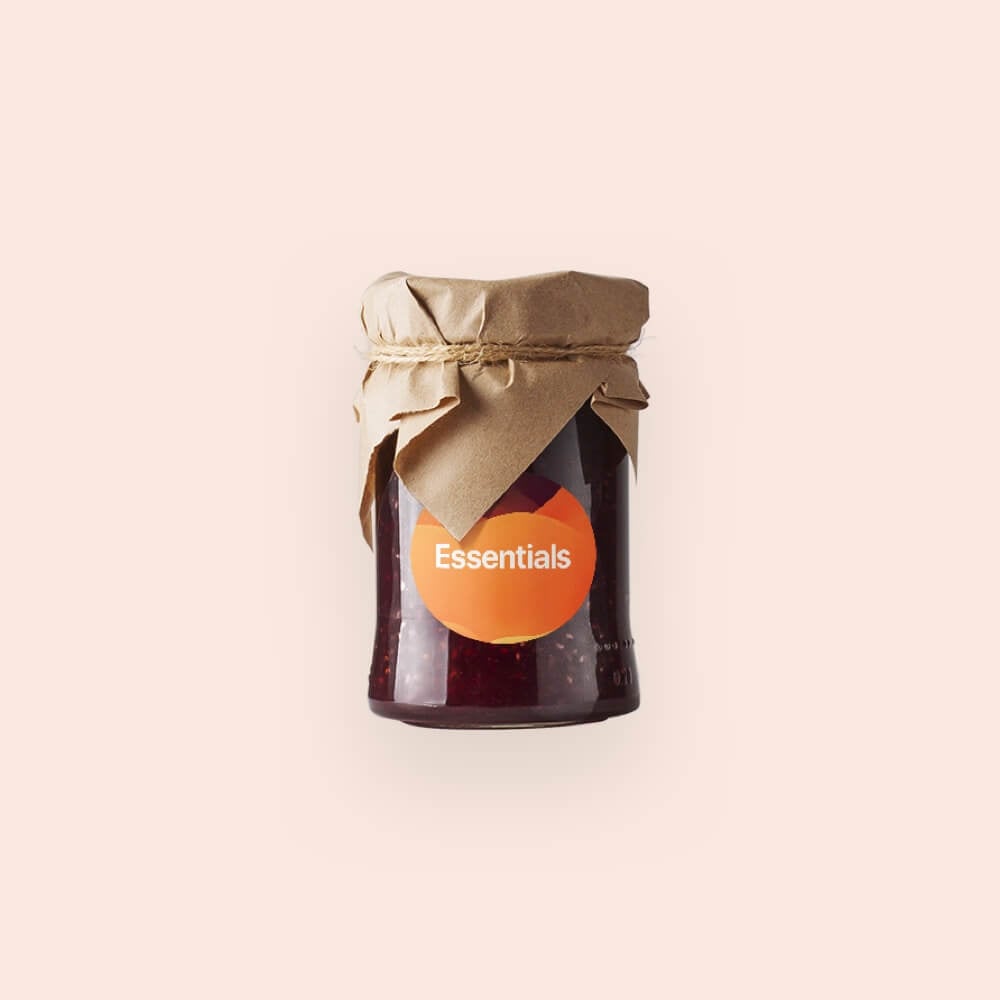
Continuous impingement drying of coated webs & printed substrates
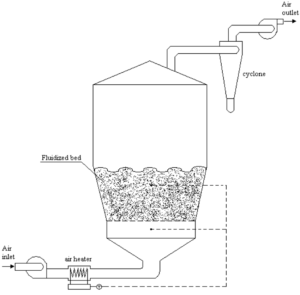
Continuous impingement drying of rubberized coir products like mattresses
Semi-continuous batch drying of agricultural material
Batch fluidized bed drying of granular material like CTC tea, pharmaceutical products.
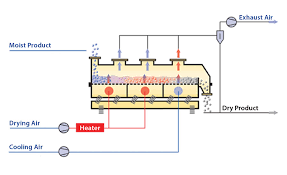
Continuous fluidized bed drying of CTC tea and other large volume products
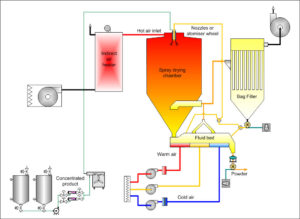
Continuous spray drying of nutraceutical products, instant tea, detergents
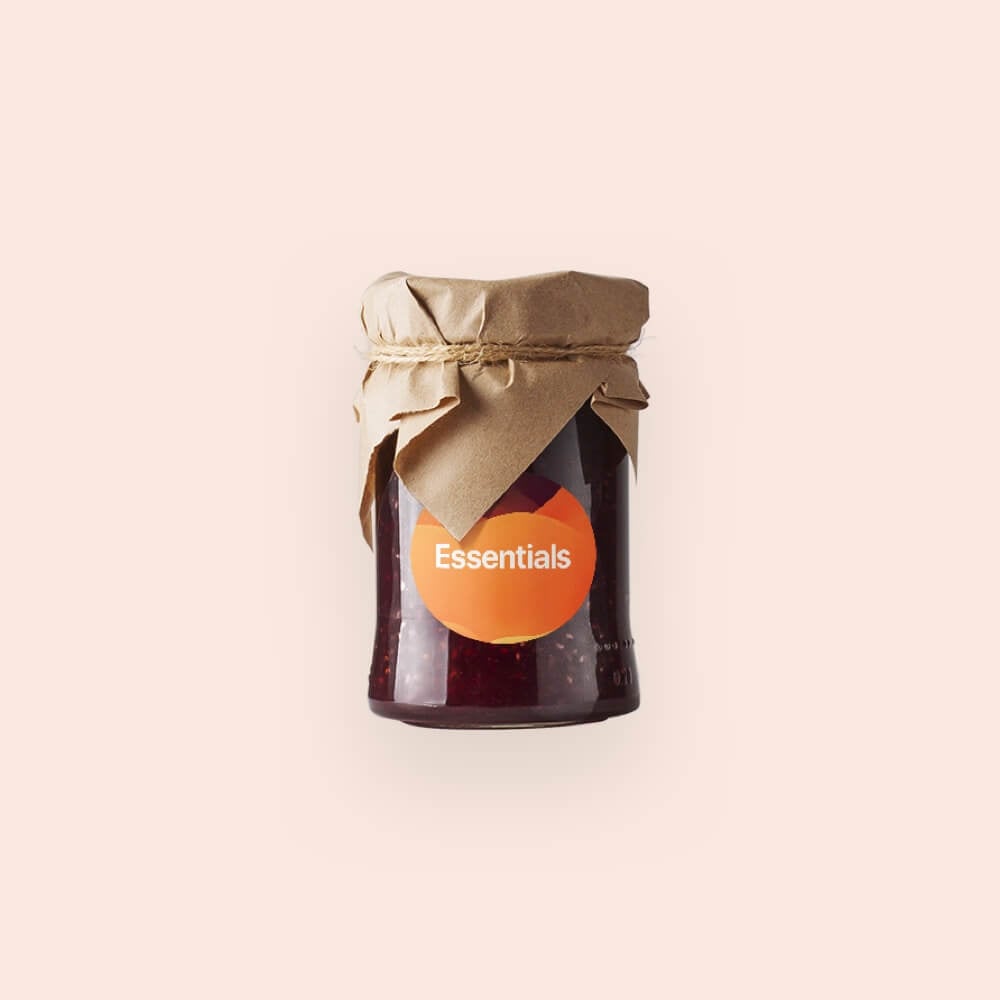
Continuous double-drum drying
Minimize your drying cost through optimized design of hot air generation syste
Drying systems engineered by ChemiProcess are optimally designed to meet the requirement of solvent evaporation in rotogravure printing , laminating and coating machines
- Hot air at the temperature and flowrate specified
For respective drying hoods are generated through - Heat exchange between air and hot thermic fluid.
- Capacity rating for the thermic fluid heating systems
In terms of `Kcals/hour’ are arrived based on maximum heat demanded by the machine - Detailed engineering activities include preparation of P & I Diagrams, mass and energy balance diagrams,
- Piping and hot air ducting layouts through optimized space management depending on space availability within the plant
- Design and engineering of local exhaust systems ensures odor free working atmosphere within the plant in case this is not provided by the machine suppliers as a part of the printing /laminating machines.
- Depending on the requirement of heat supply specified by the machine manufacturer, design and detailed engineering is undertaken considering hot air generators without the necessity of thermic fluid being circulated in the circuit.
- Finned tube heat exchangers are designed and detailed for hot air generation using hot thermic fluid
- Blower motor ratings for the drying system are kept at minimum through systematic pressure drop analysis

Minimize your drying cost through optimized design of hot air generation syste
- We design and detail high efficiency LPG fired thermic fluid heaters with proven capability of operating at thermal efficiency over 90% can be integrated with flexible packaging machines to reduce drying cost.
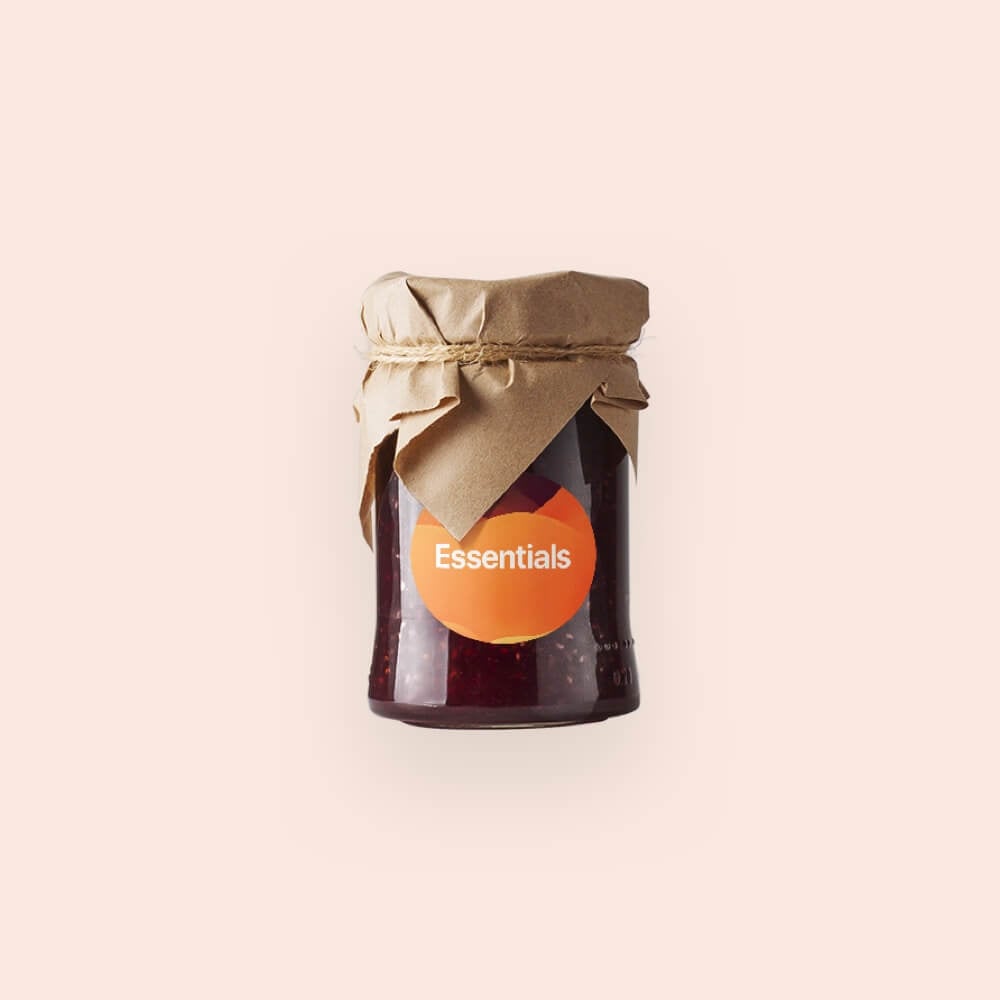
- We provide comparative assessment of using various fuels like diesel, LPG, natural gas, firewood, depending on site conditions and fuel availability
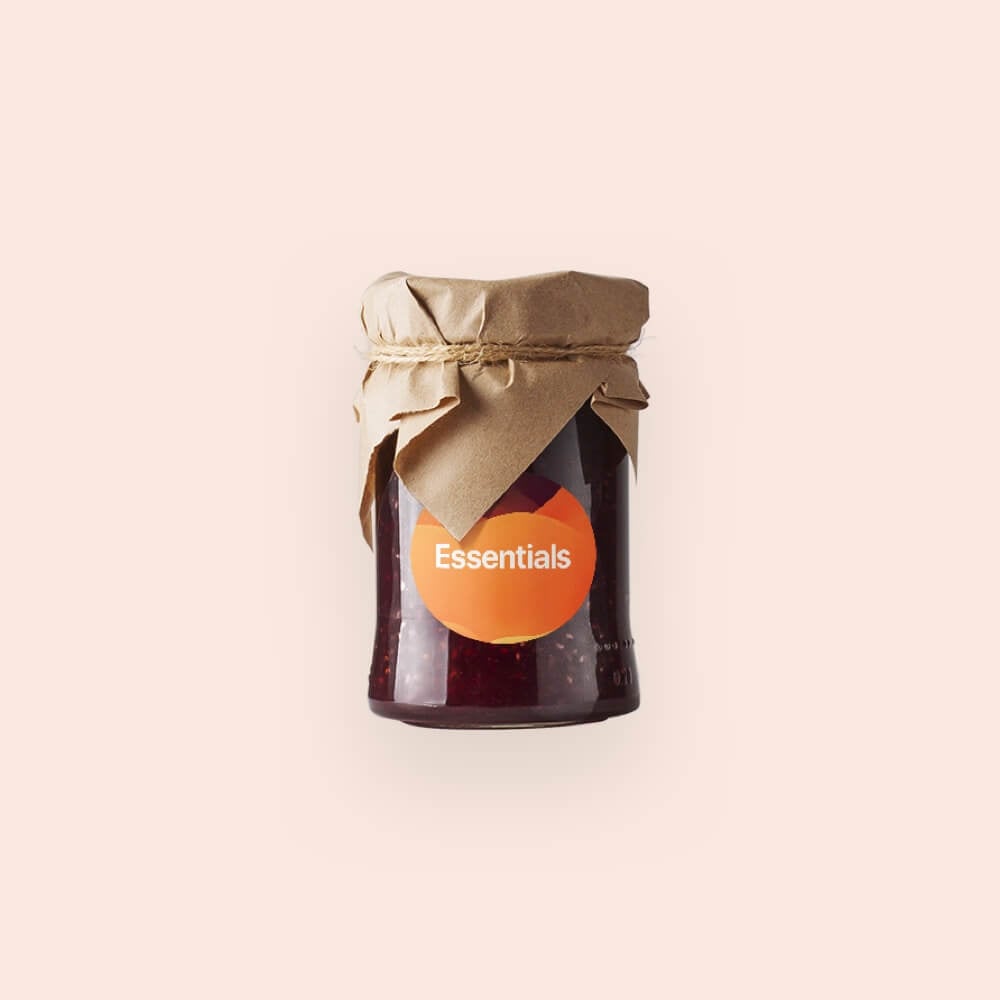
Drying systems designed by ChemiProcess Incorporate exhaust air recycle to minimize fuel consumption
- Though the temperature of hot air at exit of drying hoods is lower than the supply air temperature, it is still high enough to save energy if recycled back to mix with the fresh air at ambient temperature. This is achieved through carefully designed damper control system which can maintain the recycle ratio at the optimum level to maximize energy saving without risking the operation due to excessive buildup of solvent in the hot air circuit
Drying systems designed by ChemiProcess Incorporate exhaust air recycle to minimize fuel consumption
- Recycling exhaust air containing organic flammable solvents is accompanied by the risk of increasing the concentration of solvent in the air to levels that may make it potentially explosive. Organic solvents have a lower explosive limit ( LEL) and a higher explosive limit (HEL). In the event of the solvent concentration being between LEL and HEL, the solvent-air mixture is potentially flammable. This would mean that it has a high probability to catch fire in the event of coming in contact with a source of fire like a spark generated from short circuit or friction, etc.A solvent-air mixture is expected to be theoretically safe as long as the concentration of solvent is less than the LEL. Established standards however stipulate the actual solvent concentration to be within 25 % of the LEL to prevent any uncertainty. This limit is however allowed to extend upto 50 % in case reliable solvent sensors are provided in the air stream.
- Thus, an optimally designed exhaust air recycle system incorporating solvent sensors enables the exhaust air recycle to be controlled at around 50 % LEL whereby the fresh air requirement and hence heat load demanded from the heat exchanger is minimized while ensuring safety.
- We provide recommendations to choose cost effective solvent sensors out of the various types like catalytic, Infra-red, flammability and others depending on the application.
Drying systems designed by ChemiProcessare based on physical audit on-site that ensures mass balance with respect to air and solvent to ensure balanced air flow.
- We undertake engineering audit of existing drying systems to assess the drying efficiency, air balance and solvent balance.
- Based on measurements of solvent concentrations, air flowrates in the various exhaust air streams, and quantity of solvent that is transferred to the web alongwith the ink or coating as input to the drying system, the quantity of solvent escaping out of the machine into the shop floor can be estimated. Solvent audit thus carried out paves the way towards conservation of solvent loss through tight control of the machine design and operation.
ChemiProcess undertakes feasibility analysis and provides engineering support for implementation of solvent recovery system
- With adequate knowledge and necessary expertise developed in the area of exhaust air recycle control, we are in a position to help minimize escape of solvent out of the machine and maximize the solvent concentration in the exhaust air leaving the drying system, thus making it suitable for cost effective solvent recovery.
- Of the two approaches viz.
Approach-1: recovering thermal energy from the VOC laden exhaust air through combustion in Oxidizers, and
Approach-2: solvent recovery,
the latter is by far the more profitable and environment friendly approach. The profit apart, solvent recovery helps prevent contaminating the environment with organic vapors whereas VOC oxidation increases the content of carbon dioxide, regarded as one of the greenhouse gases, in the atmosphere.
ChemiProcess undertakes feasibility analysis and provides engineering support for implementation of fuel saving through solar energy augmentation.
Excellent opportunity lies fairly untapped whereby fuels saving can be achieved in a drying system by harnessing solar energy.to supplement the heat input to a thermic fluid circuit.
Parabolic Dish Collector (PDC) or Parabolic Trough Collector (PTC) systems help converge the incident rays from the sun to the focal point where a receiver receives the reflected rays. Thermic fluid circulated through the receiver, picks up the heat incident on the receiver. The heat thus picked up by the thermic fluid in the primary circuit can be transferred to the secondary circuit carrying the thermic fluid that passes through heat exchangers in the hot air drying system.
